Turning Designs into Great Guitars
Turning designs into great instruments isn’t easy. Technical drawings can’t convey the intended tone of an instrument, or the construction methodology required to create the desired characteristics and sound. Before building a new guitar can begin, the plans and intentions of the designers are discussed with the craftspeople at the factory in order to develop an appropriate production process. Every guitar is different, and coming up with the ideal production methodology and workflow for each guitar is critical.
Overdoing It
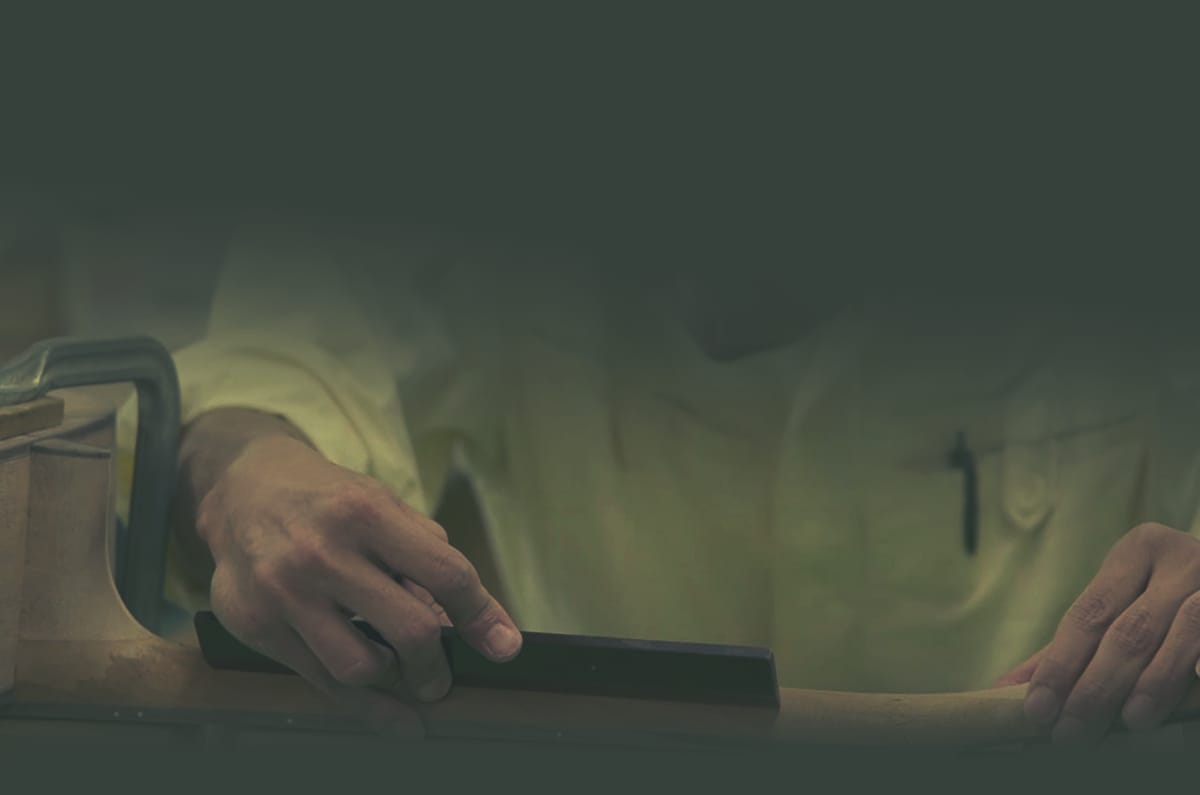
Sometimes “overdoing” things is the only way to ensure that the desired quality is achieved consistently and in every possible situation. Yamaha takes manufacturing details to extremes in many cases, but the final results are worth it. The Yamaha process of pre-matching acoustic guitar bodies and necks before finishing, where the neck and body are matched up early in the crafting process, is one example. Experience has shown that the quality of the neck-body joint plays an important role in maximizing the instrument’s tone and response; in short, the fit must be perfect with intimate contact between neck and body. The level of control and consistency that comes from building and finishing the neck and body as a matched pair is worth the extra effort.
An Ideal Blend of Machine Precision and Human Skill
There are some tasks that are best left to machines, particularly those that require extreme precision and repeatability; for example, cutting the fret slots in fingerboards is a critical job that is handled by precision computer-controlled machinery. But in order to deliver instruments that really meet guitarist’s needs there are elements that require individual attention and flexibility. That’s where the skill and experience of Yamaha craftspeople really shines.
The Finishing Touches
Yamaha works hard to ensure that every guitar and bass leaves the factory in optimum playing condition. Some players may want to make minor adjustments to match their individual playing style, but important details such as fret levelling and finishing are taken to custom-shop level right at the factory. Final assembly is a production step that requires the utmost care if optimum tone and performance are to be achieved. Parts that are not properly aligned or not solidly attached can degrade both sound and playability, so assembly workstations and processes are designed and set up for smooth, efficient assembly so the builder can concentrate fully on achieving perfect results.
Crafting the Tools
Most of the tools used for making guitars have to be made by hand for the purpose, and many are created specifically for a single model and won’t be used for anything else. Developing tools and jigs that make it easy for guitar builders to consistently produce perfect instruments is an important element of Yamaha’s approach to craftsmanship, but tools and jigs can wear and go out of alignment with use, so special care is taken to keep them maintained and in perfect working condition at all times: it’s a hidden but vital part of overall quality control.
Keeping the Craft Alive

Because of the reliance on skilled craftsmanship in the making of fine guitars, the only way to ensure consistent, continued quality into the future is to pass the know-how on to the next generation of craftspeople. This kind of skill can only be fully passed on person to person, through hands-on apprenticeship, so Yamaha makes this an official part of the guitar manufacturing process. The team of guitar builders changes with time, but Yamaha is dedicated to ensuring that the basic skills, as well as the many innovations developed along the way, are effectively passed on so that Yamaha guitars can continue to evolve.
The guitar making process
RESEARCH AND DEVELOPMENT
CRAFTSMANSHIP
QUALITY CONTROL
ACOUSTIC ANALYSIS
ACOUSTIC GUITAR ANATOMY
ELECTRIC GUITAR ANATOMY
MAINTENANCE: CHANGING YOUR STRINGS